Through sandblasting, the abrasive properties of sand turn to smoother surfaces with minimal visible faultiness and flaws. It is similar to sandpaper that when rubbed against an area, the sand removes some of the top-layer material. It is thereby producing a smoother texture.
Abrasive blasting makes surfaces ready for coating applications. Keep the temperatures or relative humidity levels low using temporary climate control solutions. It eliminates excess moisture that may hinder the protective coating’s application and drying. Exposing the bare metal to the environment makes it susceptible to oxidation. So the temperature and humidity control is essential when preparing metal surfaces.
A sandblasting machine has a compartment on top where the sand is dispensed. It is connected to a conventional air compressor hat. By activating the air compressor, the sand propels through a handheld nozzle. The pressure of the sand may vary depending on the settings. It can range from 50 to 130 pounds per square inch (PSI).
Sand is “blasted” across the surface with its abrasive properties. It produces a smoother surface. One best example of sandblasted material is concrete. It is treated with sandblasting after the concrete has been poured and allowed to dry. The process gets rid of some of the excess material on the concrete thus makes it smoother.
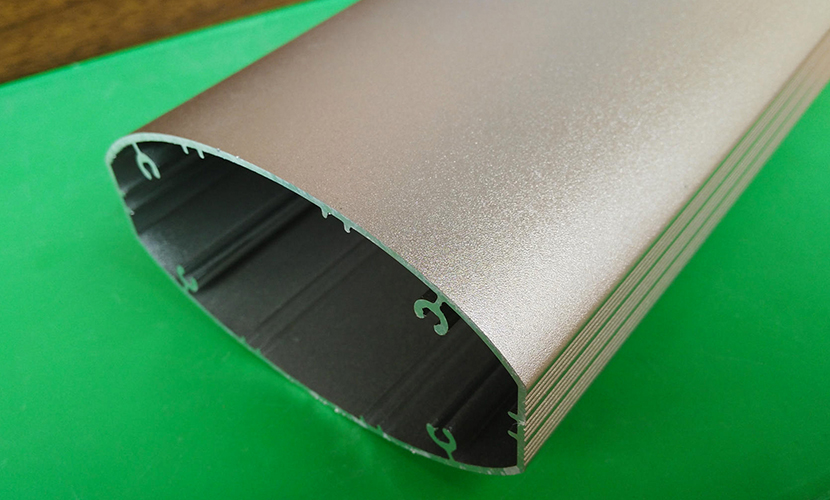
What to consider when sandblasting aluminum profiles?
Here are some pro tips that we can share.
Tip #1: Choose an appropriate sandblast media.
Glass beads and baking soda are best for strip coatings that do not cause harm to the surface. Use crushed glasses or aluminum oxide when there’s a need to leave a profile for a repaint. Although aluminum oxide is more expensive than crushed glass, it is faster. We do not recommend the use of steel-based blast media with aluminum surfaces. It will impregnate the aluminum surface and cause corrosion. Use glass bead media for a polished look. Other options may affect cost-effectiveness and the end appearance of the product.
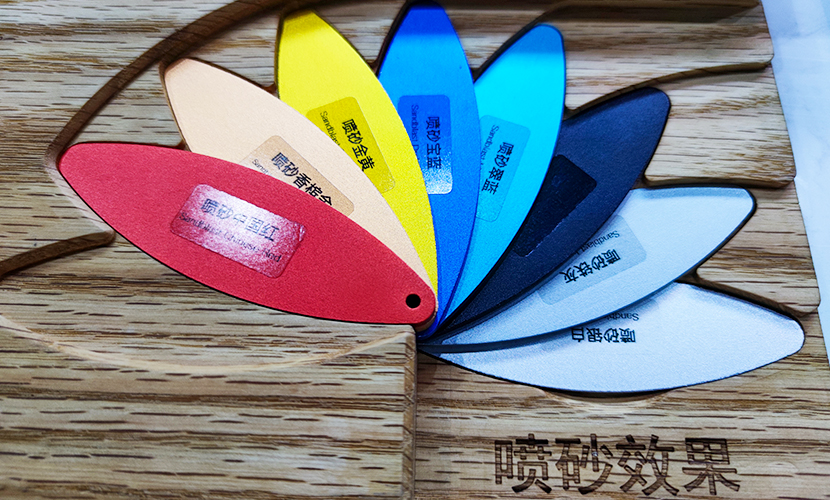
Tip #2: Apply sandblasting pressure.
There is a potential use of aluminum panels in thinner thicknesses. Thus, there’s a tendency for them to be potentially susceptible to warping when blasted. Warping or creating significant indentations in the product’s surface can be avoided by starting the pressure set very low and gradually increasing. It results in a blasting pressure of around 50 – 60 PSI.
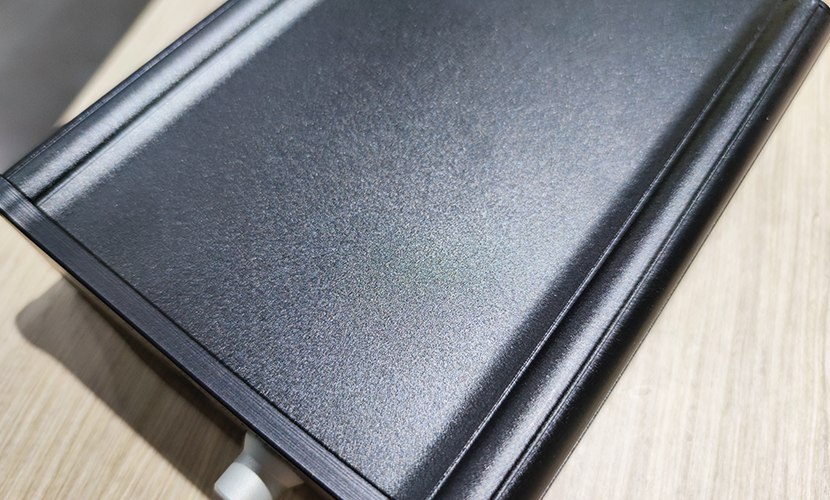
Tip #3: Complete a small spot test.
Each specific project has its unique factors to consider. Completing a small test blast will definitively result in a given blast media. In addition, pressure will provide how long it will take to blast. It helps the proper bidding of the blasting work and ensures a likable result of the media and pressure chosen.
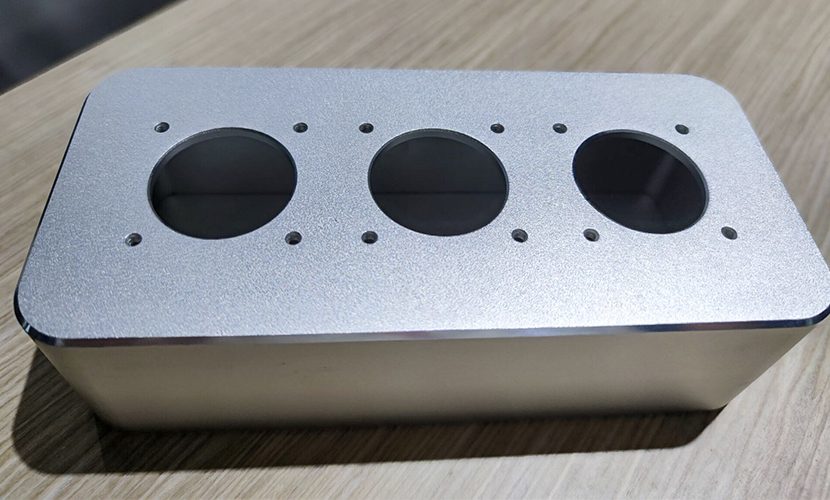

What makes sandblasting beneficial?
Sandblasting is inexpensive and reusable. It offers additional economic advantages. It efficiently cleans surfaces cleans better and faster than traditional techniques. This process can remove rust on metal surfaces.
The workpiece surface has a certain degree of cleanliness and different roughness due to the impact and cutting action of the sand.
Sandblasting improves the mechanical properties of the aluminum profile surface. Furthermore, the following makes this kind of surface finish a total package: enhances fatigue resistance of aluminum profile, increases the adhesion between it and the coating
prolongs the durability of the coating, the flow of paint, and decoration.
This kind of surface finish has its unique challenges. To sum up, we can get the best results through these steps: choosing a blast media that is suitable such as glass bead, soda, or aluminum oxide; starting at low pressure and gradually increasing it; completing a test area before blasting the entire product’s surface.
In every process, there will always be issues to happen. It may be complex, sophisticated, rigorous in handling metals like aluminum. Hence, proper, careful, and intelligent steps in selecting, combining, and applying the materials produce the best result.
For your aluminum needs, Yongu offers customized products. Check out our product page to see what we can offer or reach us at ([email protected]).