These aforementioned products are made up of aluminum. And before we can use them, they undergo processes like anodizing.
Let’s take a closer look of the step-step process. Anodizing aluminum enclosure.
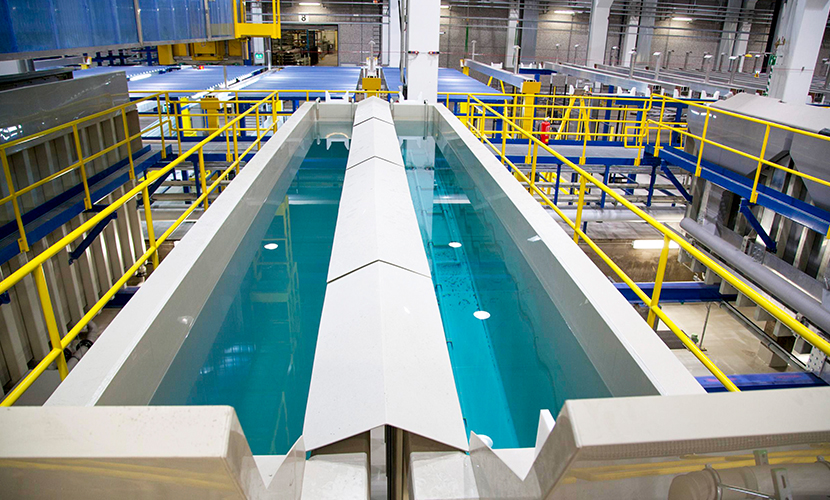
Anodizing is an electrochemical process which converts the natural oxide layer on the surface of metals into a long-lasting, corrosion proof aluminum oxide finish. This type of finish makes the metal durable, thick, and does not wear off easily. Anodizing metal means highly controlling the enhancement of oxidation – an occurrence that already happens naturally.
Aluminum is the ideal metal to be anodized since its natural compositions makes it a durable material to begin with although anodizing is also possible for non-ferrous metals like magnesium and titanium. The anodized finish meets the characteristics that need to be considered when selecting a high-quality material to be used in various essential and luxury items like kitchenware, speakers, watches, as well as interior design and constructions.
Anodizing is a much-preferred process of coating or coloring metal because it is integrated into the metal rather than just applied on top of the surface like basic paint. Plus, it provides corrosion resistance and is an environment-friendly method of producing high quality products. In anodizing aluminum, the natural process of oxidation is enhanced with high control. The process consists of 5 steps: cleaning, etching, anodizing, coloring and sealing.
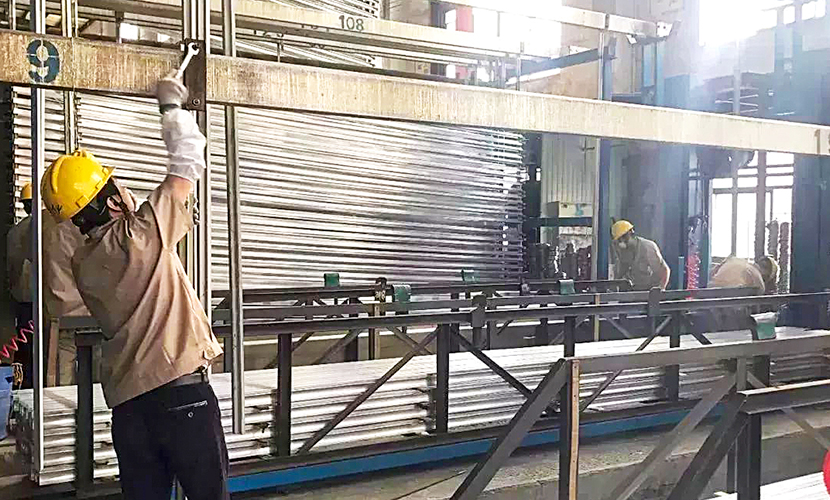
Step 1# CLEANING
Pre-treatment cleaning is done by submerging the aluminum to an alkali or acid-based detergent bath. Doing this will remove any excess grease and oil from the extrusion process - important for an even etching of the metal surface without spots. When cleaning is done, the metal is rinsed as a preparation for the next step.
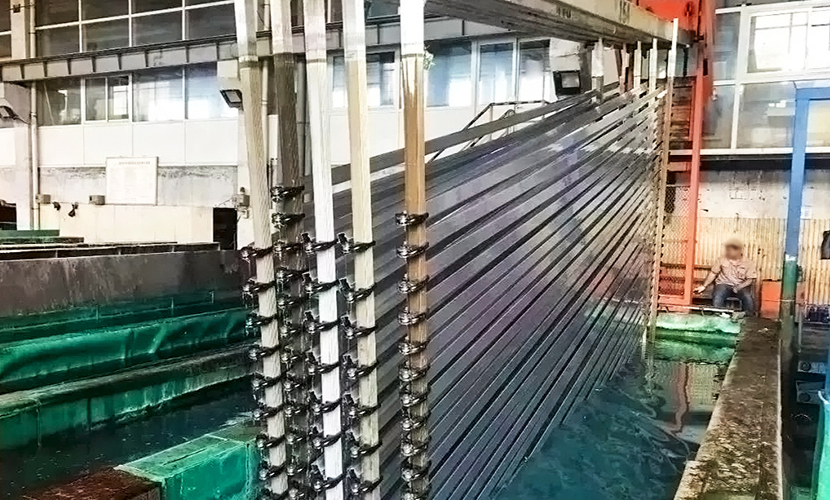
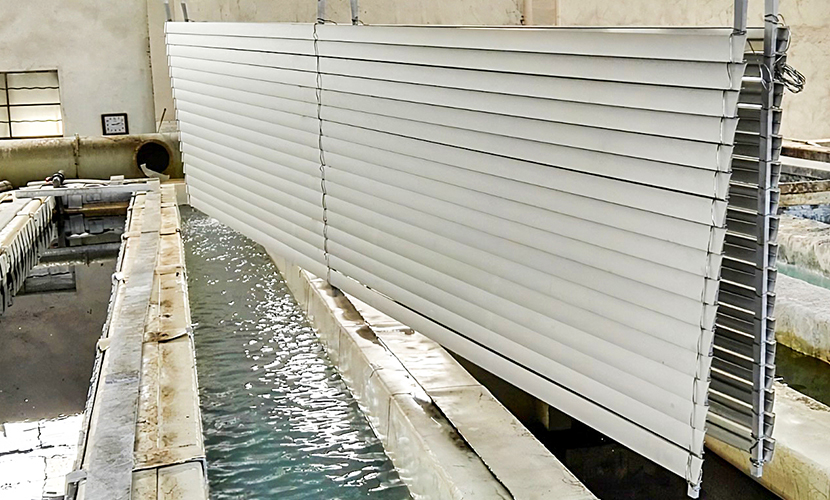
Step #2 ETCHING
Caustic or acid etch is used to remove minor imperfections and prepare the surface for the next stage. In this step, a thin layer of aluminum material is removed to create a uniform surface ideal for anodizing. The etching process also provides the uniform matte finish, seen in the final product. The material is then rinsed again in preparation for the anodizing step. This rinse is known as de-smutting and is designed to remove any residue from the etch process.
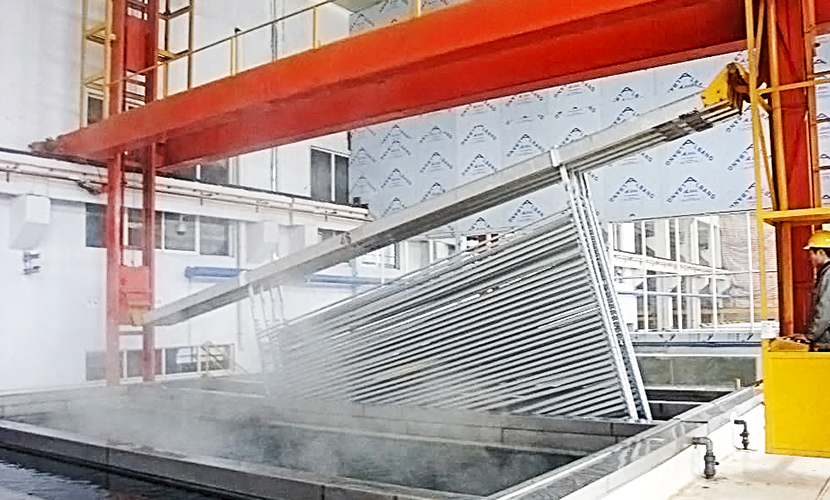
Step #3 ANODIZING
After additional rinses, the material is now transferred to the anodizing tank and immersed to the electrolyte of uric acid. An electric current pass through the tank causing the release of oxygen ions and the growth of the anodic coating. The anodic coating grows the substrate and grows outward creating a fully integrated layer. The anodizing process generates a lot of heat so the electrolyte must be refrigerated to maintain the proper temperature immersion time is carefully monitored since this is how the desired thickness of the coating is achieved. Periodic testing ensures the proper results.
Following anodization, the material is rinsed in deionized water to remove all minerals that could cause spotting during the final steps.
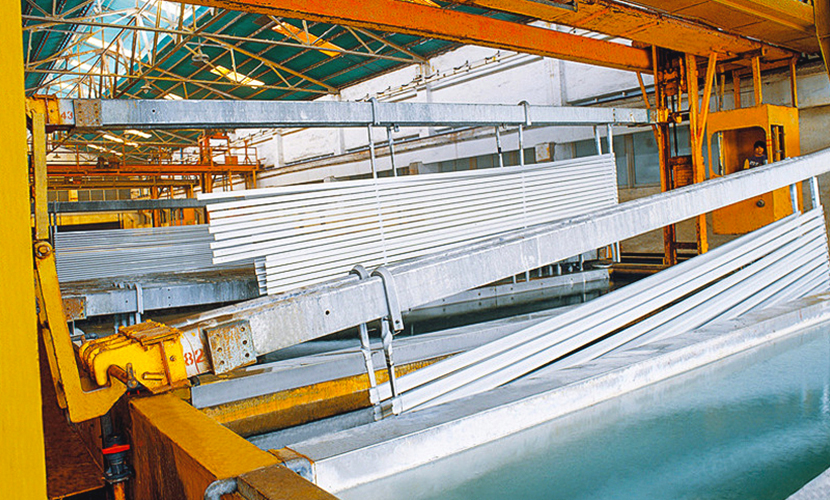
Step #4 COLORING
If the product requires color, it will be added at this stage. The newly created anodic coating is a porous structure, these pores will be the space for the dye to sit in and integrate with the anodic coating. Dissolved metal salts or organic dyes can be introduced into the open pores to create various shades.
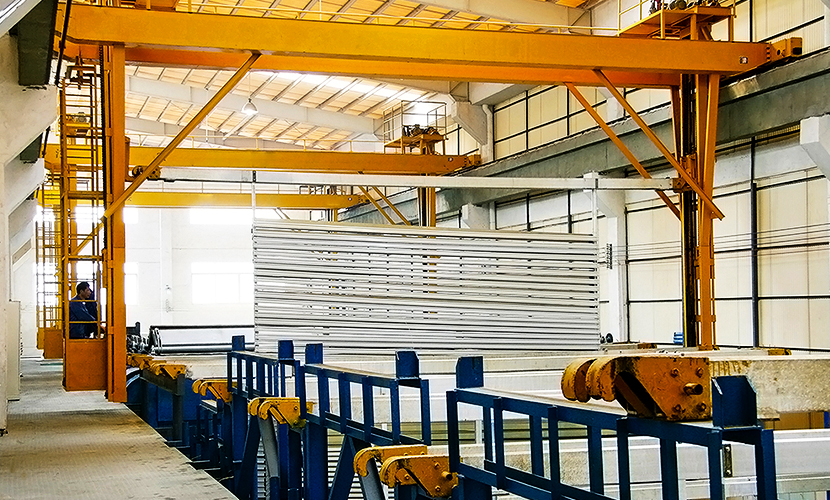
Step #5 SEALING
The final step of the anodizing process is to seal the porous using a solution of nickel acetate. Sealing closes the pores, allowing the dye to stay and provides a uniform surface. This final sealed surface is very durable and provides color that is long lasting and integral to the surface.
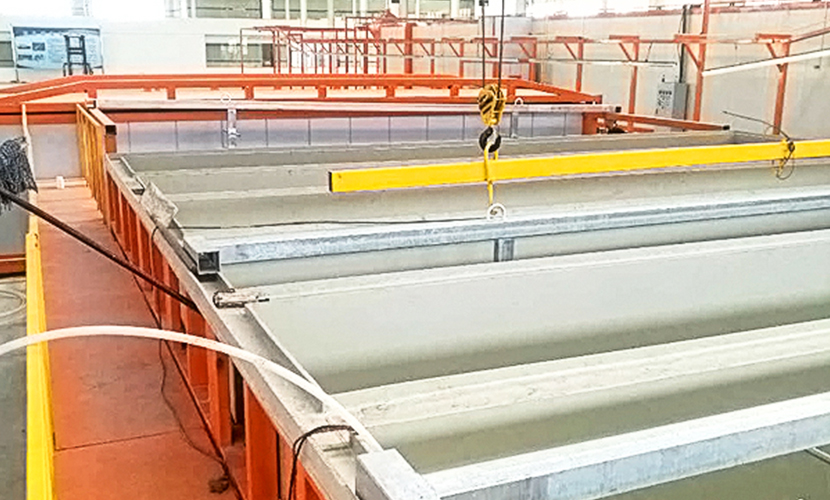
This simple method of anodizing guarantees many advantages to the producers, consumers, and even the environment. For almost 100 years since this concept was created, the process of anodization has been continuously refined but it’s purpose to create quality materials remains unchanged. The existence of modern technology definitely improved the quality of anodization. Through the observation done by United Anodizers, it was proven that modern buildings that utilized anodized materials withstand the durability test for over 40 years. Anodized products are top-tiered when it comes to corrosion resistance, abrasion resistance, safety from adhesion failure, fading, chalking, and also filiform corrosion.
On top of that, colored anodized products still meet the aesthetically challenging taste of today’s consumers. The natural metallic sheen and feel of the aluminum is kept during the process. Giving the product an anodized finish will further enhance the natural beauty of aluminum while showing off its vibrant surface when interacting with natural or artificial lighting. Dyeing the surface offers a wide variety of colors and shade which is an advantage on choosing the color of your choice. The uniform surface finish seals off a pleasing elegant look for all metal shapes and textures.
The use of Aluminum and the process of anodizing benefits the environment. Aluminum can be recycled through re-melting with minimal loss for every cycle. Recycling only consumes 5% of energy that is required in producing primary aluminum and does not join any chemical processes and emission. Anodizing aluminum may be simple but drastically wins over other finishing methods since it only requires pure aluminum, alloying elements and oxygen. Modern anodizing plants meet the current environmental standards. The process does not require chromating which is an environmentally sensitive pre-treatment. Anodizing has no by-products like Carbon Dioxide (CO2) or solvent emissions. This is a win-win situation for the environment and mankind.
Here are some end products of anodized aluminum that we often use:
- Appliances such as refrigerators, dryers, coffee brewers, ranges, televisions, microwave equipment.
- Building exteriors, such as storefronts, curtain walls and roofing systems.
- Display cases, pans, coolers, and grills for the food industry
- Exterior panels for aerospace vehicles, clocks and electronic products, fire extinguishers, photo equipment, solar panels, telephones, picture frames, and bathroom accessories
- Golf carts, boats, and camping/fishing equipment for the leisure industry
- Hundreds of components for motor vehicles of all kinds such as trim parts, wheel covers, control panels, and name plates
- Tables, beds, files and storage chests for homes and offices
- Vents, awnings, dust covers, light fixtures, storm doors, window frames, mailboxes, bathroom accessories, patio covers, and wall switch plates for buildings
From these examples, we could see how much aluminum we are actually using today and how these all make sense in our everyday lives.
Anodizing is a highly-beneficial industrial process. An environment-friendly method of producing durable and long-lasting products which also pleases the eye of consumers. Utilizing the modern technology while keeping the natural laws of science to meet the market demand.
Yongu always make sure that our products and processes are less harmful to our environment. Check out our products here. https://www.yg-enclosure.com/