In today's article, the YONGU team explains the importance of efficiency and how a heat sink electronic enclosures could improve your machinery's functionality, effectiveness and utilization.
UNDERSTANDING THERMAL DISSIPATION
Managing heat is one of the biggest obstacles when developing any electrical product. The built-up heat within the electronic enclosures is hazardous to the electronics inside. Overheating can shorten a product's useful life and even cause it to break down. Whether you're talking about a lightweight indoor gadget, a game controller, or a heavy-duty outdoor tool is valid.
The designer must always pay special attention to the thermal behaviour of such parts. Getting the most out of your technology investments helps you have a firm grasp of the specifics of your setup and the demands of the devices you want to use.
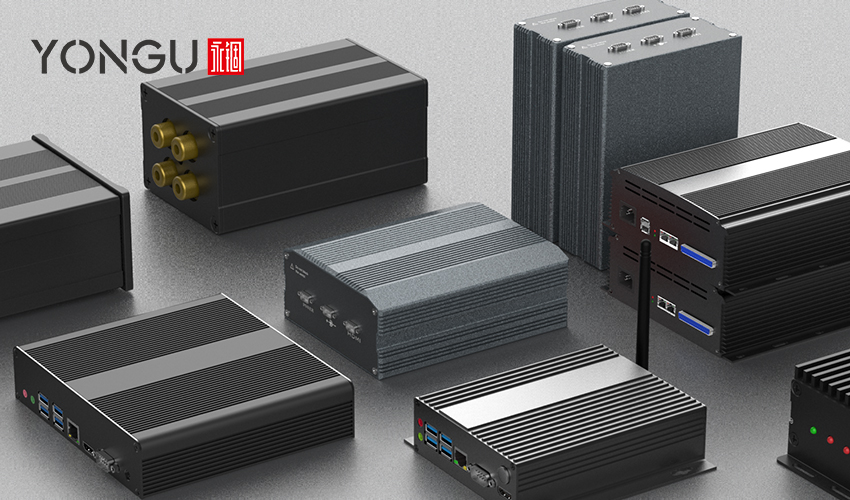
THERMAL DISSIPATION CONDUCTION
When looking at heat exchangers, it's essential to consider which design principles or implementation strategies would suit your specific setting. Let's look at the most common means of heat transfer, conduction, and convection.
- Thermal Interface Material
- Heat Sink
Typically, heat sinks are made from aluminum or copper due to these metals' high thermal conductivity and the inherent correlation to heat dissipation efficiency. Since surfaces are responsible for transmitting heat, heat sinks come in various designs to maximize contact areas.
- Heat Pipes
- Thermoelectric Modules
- Thermal Grease Or Adhesives
A designer has several options to consider. While dependable and effective heat dissipation is essential, it is not always simple to find the optimal mix of components to achieve this goal. If you need heat dissipation, one of the most common methods is to install a fan in the heat sink electronics enclosure.
HEAT SINK ENCLOSURES
Aluminum instrument enclosure is used to dissipate the heat generated within a metallic housing. The extrusion process allows for the production of heat sink metal enclosures in any desired length and with any desired protection class (IP67 or IP68). Electronic devices that create a lot of heat, such as power systems, compact computers, and microprocessors, benefit significantly from being housed in metal heat sink enclosures.
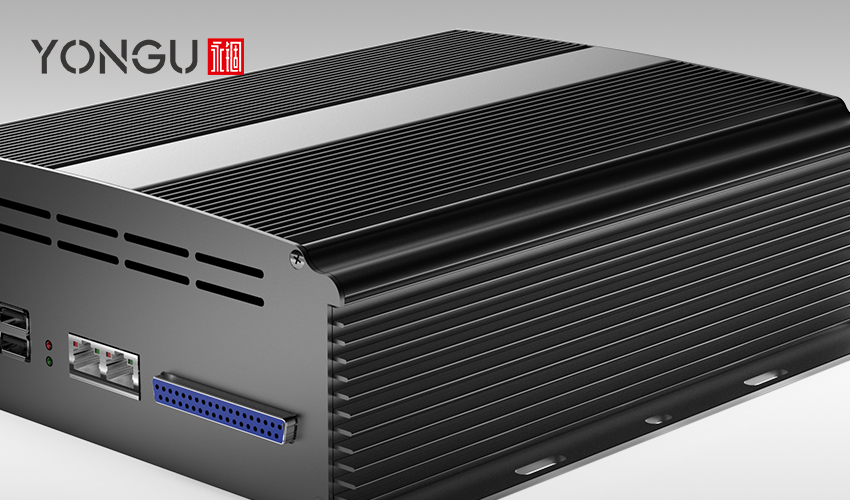
BENEFITS OF HEAT SINK ENCLOSURE
Composite Material
Recognizing the significance of composition material in customized heat sink electronic enclosure cooling is crucial. For instance, aluminum is commonly used in heat sinks since it is thought to be the most effective material for thermal management. Still, it's important to remember that alternative materials are even more efficient sometimes.
Copper is occasionally used in place of aluminum because its heat transfer rate is almost twice as high as that of conventional aluminum designs. Since industrial applications can cool down considerably more quickly, cycle durations can be decreased, yields can be increased, and the process may be optimized.
Eco-Friendly
There is also the fact that heat sink enclosure cooling has no adverse effects on the natural or working environment. There are several thermal management approaches, but few of them can simultaneously maximize performance while minimizing their impact on the surrounding environment.
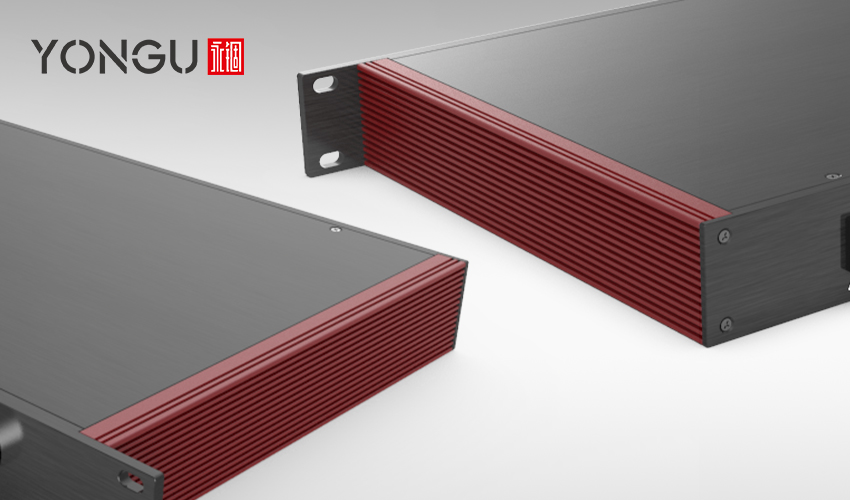
YONGU HEAT SINK ENCLOSURE
With a YONGU heat sink electronic enclosure, you'll get the best-forced air cooling available. As power densities per unit area continue to rise, heat sink allocations continue to shrink. If you're looking for a quality heat sink enclosure, go no further than YONGU. Their extruded aluminum heat sinks have an exceptional thermal transfer rate. High-quality, CNC-precision-cut aluminum is used in the heat sink's base and fins which work together to swiftly disperse heat into the surrounding atmosphere.
YONGU offers a unique heat sink electronic enclosure YONGU Design Holes Drilling Heat Sink Industry Chassis B08 364*190mm.
It has the following unique features
- The extruded side panel is an available add-on
- The flat, heat sink or stripe design for excellent heat dissipation
- Sizing adjustments for both width and length are possible
- Features anodized tones
- Milling and cutting out shapes
- Include a unique front panel
- 1U / 1.5U / 2U / 3U / 4U customized racks
For further information and customized product of your requirements, please follow our FACEBOOK for more updates and informations.
You can also contact us at +86 13326782625 or write us [email protected].