Casting and machining work to produce complicated, compact, and cost-effective components. In many circumstances, it's possible to rework welded fabrications into single machined castings. Reducing component weight, labor or welding input, and total part prices are all aims of such a layout.
Conventional vs. CNC
For more than a century, conventional machining has been in use. Setting up and operating the machining equipment requires a competent tradesperson (machinist or engineer). However, traditional machining is still employed to manufacture prototypes, installations, and low-volume production components with basic geometries. CNC machines have replaced conventional lathes, mills, grinders, and other manual-operated devices. You may be surprised to learn that this technology is older than you believe. The earliest machined tool was discovered in Italy and dated to 700 B.C., making it an interesting technical fact. Despite its extensive history, CNC machining is now one of the most revolutionary technologies in the industrial sector. It is more efficient than additive or formative manufacturing since it is digital. Prototyping and subsequent manufacture of custom-machined parts frequently make use of this technology. As a general rule, CNC machines have a long history and reputation for trustworthiness. We've been running devices for two decades without any significant problems. CNC machines are constantly improving, with new features being added by providers regularly. Machine surveillance and troubleshooting are becoming increasingly prevalent due to a recent technological push.
In computer numerical control or CNC, machining, specialized, fully automated machines are used to accomplish the various machining processes. A built-in computer manages every aspect of CNC machines. CNC code or programming is used to automate the machining process. The machining engineer or programmer generates an alpha-numerical code sequence (program) using CAD/CAM software, which controls every element of the machine's functioning during the machining cycle.
Ways CNC Machining Is Aiding Engineering & Industry
Convenience with PrecisionA CNC machine eliminates human effort, which saves time and improves the efficiency of manufacturing operations. Robotics are speedier than human workers. Using digital technology in production also makes it possible to work seven days a week, reducing human error.
More than three feet per second may be achieved using CNC machine feed with speed rates exceeding 2,300 inches per minute. Tasks like bringing the spindle home to change tools and correctly placing the cutting tool before cutting are made faster by increasing the speed. Part material, mechanism, route, and cut depth all impact cutting feed. Face milling aluminium requires a feed rate of around 5 inches per second.
CNC machines can cut with 0.001 inches because of their design and manufacture. That's a lot of nitpicking. To be more precise, cutting at a width roughly one-fourth the width of a human hair. In addition, it is completed quickly.
It's a common anxiety among workers that machines replace them at many companies. There's no need to worry about CNC machines replacing your crew; instead, they'll empower your employees and improve their work experience.
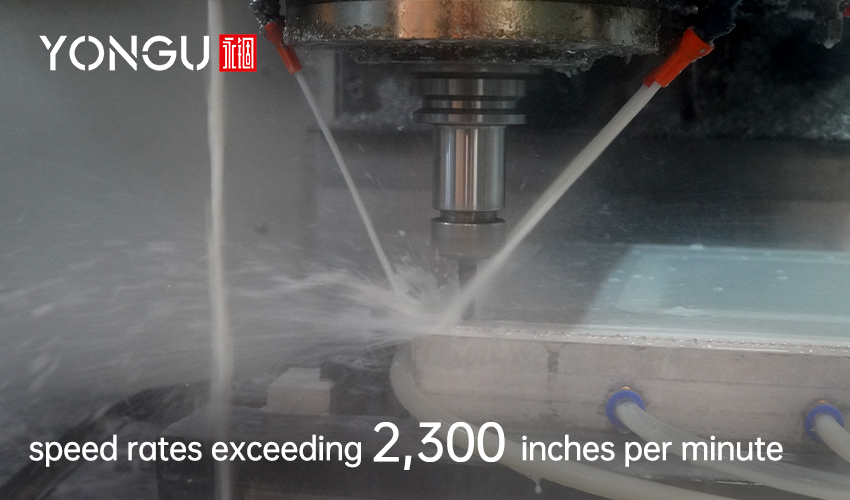
Prototype Machining
In the industrial era, prototyping is vital. It aids in the prevention of errors later on in the production process and a better understanding of the final product. Because it is time-consuming and costly, prototyping is often skipped or underinvested by firms.
Using CNC processing, prototyping is now more economical and easier to do. Mock-ups may now be made, giving producers a more precise notion of the subsequent phases in the process. The new technology makes it easier to traverse the production process and create more detailed designs.
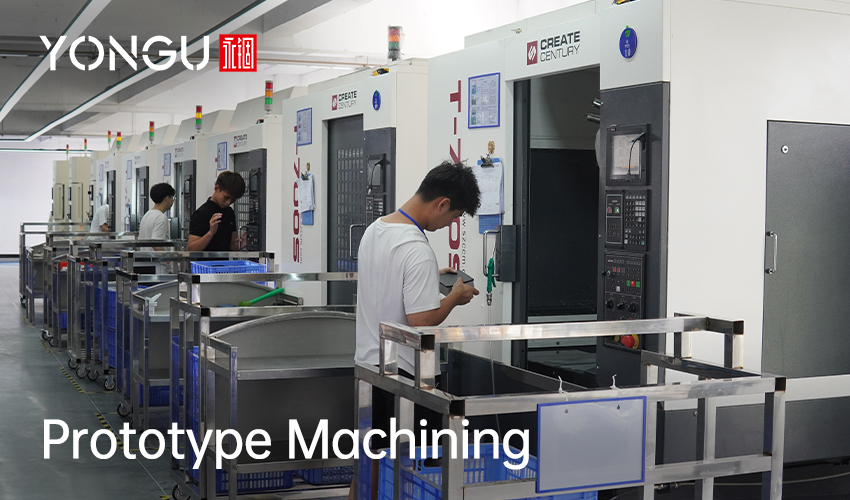
Sustainability
Different aspects of sustainability are influenced by CNC machining. Because it doesn't need as many extra resources, this method produces less waste. As a result, the probability of making mistakes is reduced, reducing wasted resources and time.
A conveyor is used to automatically remove waste material in the form of chips and shavings, and the coolant is separated so that it may be reused. The system monitors the wear and tear on the tools. By running to the estimated life of a device, the tool monitor warns an operator when a mechanism needs to be changed.
CNC machining eliminates the need for several other components like drills and sanders by including everything within the machine's main body.
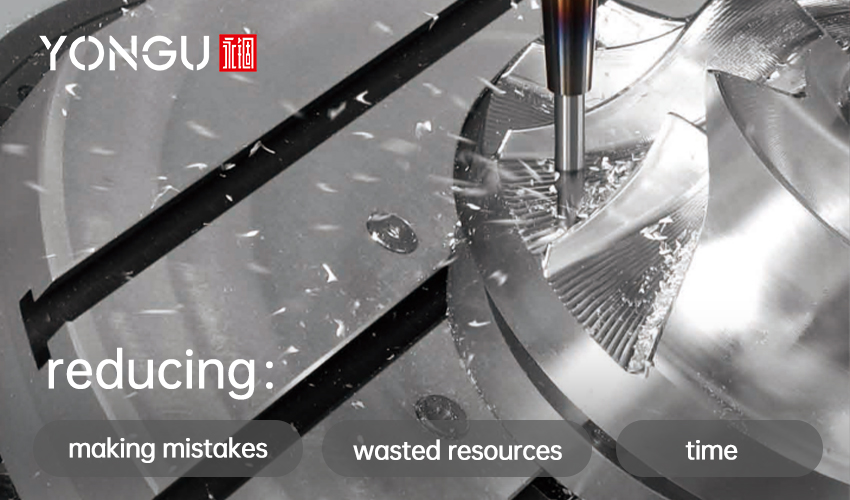
Fewer Processes with Automation
The primary components of CNC machine monitoring are computers and software. In the CAD model, desired projects are preprogrammed, and information is instantly uploaded to the device. Another advantage of this technology is that it can execute nearly all of the production phases without extra equipment or physical labor.
Tooling and process are both under the control of the software. The machine may begin cutting features and immediately switch to another tool, such as a drill, using a face mill.
Let's use a CNC machine that has two pallets automatically switched by a pallet changer to better comprehend. While the cutting area is accessible to the operator, the other pallet is inaccessible (for loading, unloading, processing, etc.). Because the machine may cut as the operator processes, unloads, and loads components, this maximizes the use of the spindle.
Hydraulic systems used to clamp, unclamp, and support parts are another example of how CNC has improved the engineering business. When the button is pressed, the parts are secured in the same order and with the same pressure. Internal consistency, uniformity, and loading efficiency are enhanced, making it ideal for use in manufacturing.
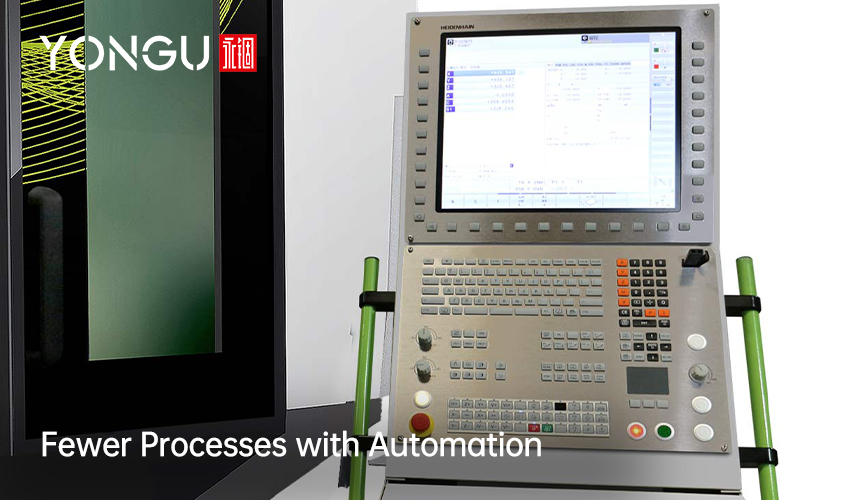
Versatility
If the item is complex, the standard tool capacity of a CNC machine can be increased to 100, 200, or more tools, depending on the machine type. A more extensive tool matrix can be employed when running many components with varied characteristics, eliminating the need to switch tools.
A CNC machine's adaptability is further enhanced by using sensors that measure and check dimensions concerning product flaws. Horizontal CNC machine centers come equipped with these sensors to identify tool failures throughout the manufacturing process. This prevents production problems from being undetected since it maintains the quality control focus on the current in-process part.
As a result of the addition of High-Pressure Coolant (HPC) to specific machines, HPC aids in creating more uniform cutting and aids in the removal of chips from a part.
Numerous other characteristics make this technology adaptable and, ultimately, transform the industry.
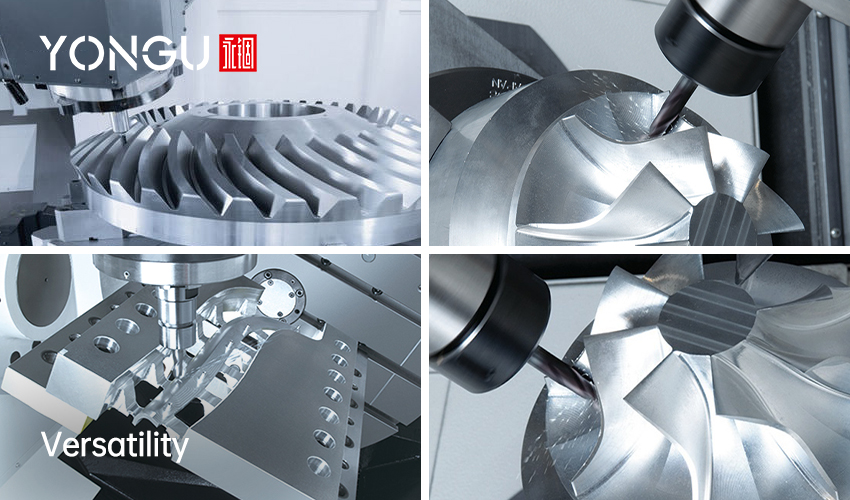
Legacy and Evolution
With a wide variety of high-quality CNC machines on the market, the competition is fierce. Fierce competition among CNC machine makers forces them to constantly improve and introduce new features at a lower cost.
When working with suppliers, a machine shop often establishes long-term relationships by getting to know the suppliers' basic demands and business strategies in depth. Suppliers are typically willing to provide innovative automation or machine customization options
to help their business develop and better serve its clients.
It is essential to use digitalization to prosper in today's environment. It makes you stand out from the competition and boosts productivity and efficiency in the workplace, and CNC is aiding a lot in achieving this.
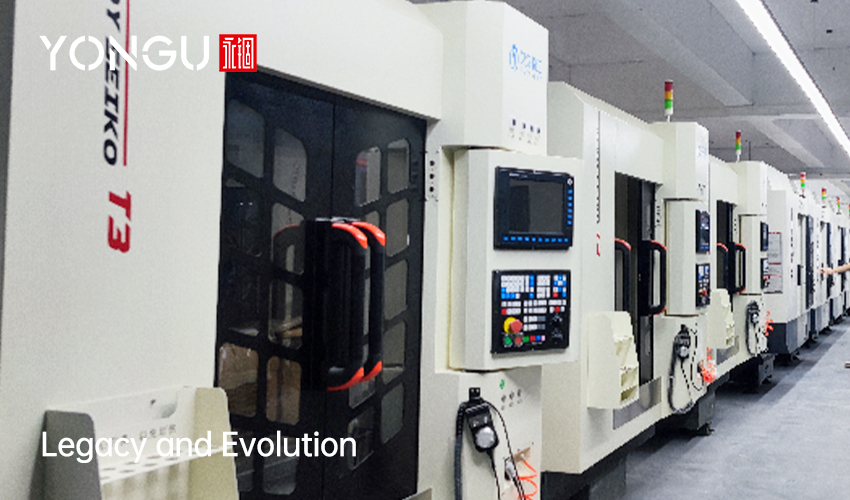
YONGU Aluminium CNC Machining Cases
The YONGU F Series CNC Machine cases contribute while designing the CNC machines as they have their benefits when merged with CNC machines which are to be used in every industry.
YONGU provides customers with the ability to customize enclosures in all three dimensions.
YONGU Rack Mount Aluminum Enclosure F02 275*128.5mm
CNC Enclosures made by YONGU provide several advantages in the production process.
- Aluminum CNC Machining Case
- Customizable thickened panels with precision processing
- Strong load-bearing capacity
- Easy Installation
- Heat dissipation is built into the side plates of the enclosure, which improves the function of heat dissipation and lends an air of elegance to the cabinet's essentially pragmatic and industrially designed appearance.
- The front, rear, and side handles and the side corners are all CNC processed to give you a technological sensation.
- Inner plates can reduce the fixing problems such as screws and rivets on the surface.
- The length, breadth, and height may all be adjusted. The length may be extended or lowered in increments of 50mm or 100mm as one unit.
- Customizable dimensions, cutout, colors, printing, etc.
- Screws use unique models to enhance your equipment safety.
- The rubber foot pads can be slip-proof and moisture-proof and have a protective effect on internal components.
For further information and customized product of your requirements, please follow our FACEBOOK for more updates and informations: https://www.facebook.com/Foshan-Gof-Electronic-Machine-Co-Ltd-104706631749290
You can also contact us at +86 13326782625 or write us [email protected].