Meatal Fabrication
Metal fabrication is the process of using raw metal materials to build machines and structures. It involves cutting, burning, welding, forming to assembly in creating the final product. This type of metal works includes hardware manufacturing to architectural and structural metals. Good thing the metal fabrication industry nowadays is a nice venture for businesses, because it offers a one-stop metal fabrication shop to aid businesses in creating their desired metal product in any form and any number. Hows and comparisons of metal fabrication processes.So, now let us go to the commonly used type of metal fabrication.
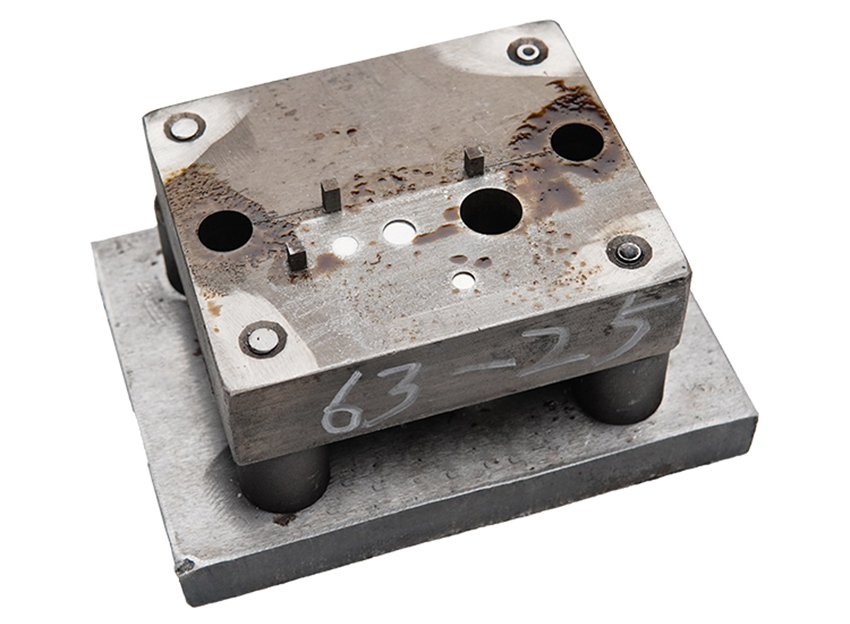
What is Extrusion?
Extrusion is the most common process for fabricating parts for fluoropolymers and metals. In a common plastic deformation process, extrusion includes a block, consolidated powder, or billet bulk material of metal to be reduced in cross-sections. Under high pressure, these bulk materials of metal are forced to flow through a die orifice. But unlike the process of injection molding, the result of extrusion is an intermediate article that requires more processing for an end product. While in thermoplastic polyesters (TP), extrusion involves heating the TP that may be in the form of beads, flakes, pellets, powders. As this TP goes inside the hopper of the extruder, it uses plasticity to melt the plastic. A plasticator is a spiral screw that rotates within a heated barrel or a cylinder. Then the melted plastic is forced through a die to create the desired product shape. There is a single screw extruder, twin-screw extruder, and multiple screw extruder that is primarily used for mixing and homogenization since this process of melting is very critical. These types of extruders are used for heat-sensitive materials for plastic compounding, such as PVC, reactive processing, plastic devolatilization, and processing of difficult-to-feed materials. However, in our case, where metal is our primary product, extrusion for metal such as aluminum, copper, steel, magnesium, and lead goes through the same process. There are different types of metal extrusion and these are direct, indirect, hydrostatic, lateral, hot col, and impact extrusion.
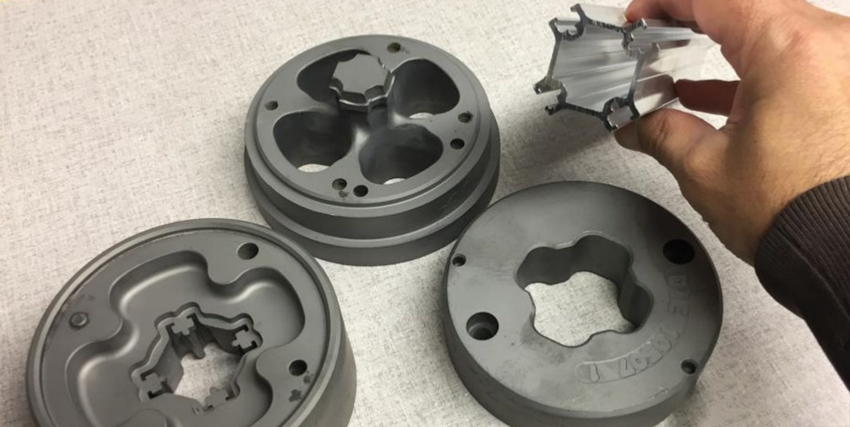
What is Die Casting?
Die casting is a necessary process for metal manufacturing, and is used in the modern industrial field. It is an economical way of making large quantities of products. Die casting can produce complicated-shaped products of light metals with high precision. Also almost half of the aluminum alloy produced globally is through gravitational die casting. It utilizes metal molds or permanent dies. In die casting, there are three main processes included which are permanent mold casting, low pressure die casting and high pressure die casting. Permanent mold casting is also called gravity die casting, uses high-quality components in a range of low-temperature metals. However, these three processes of die casting differ in the amount of pressure that is used to force the molten metal into the die.
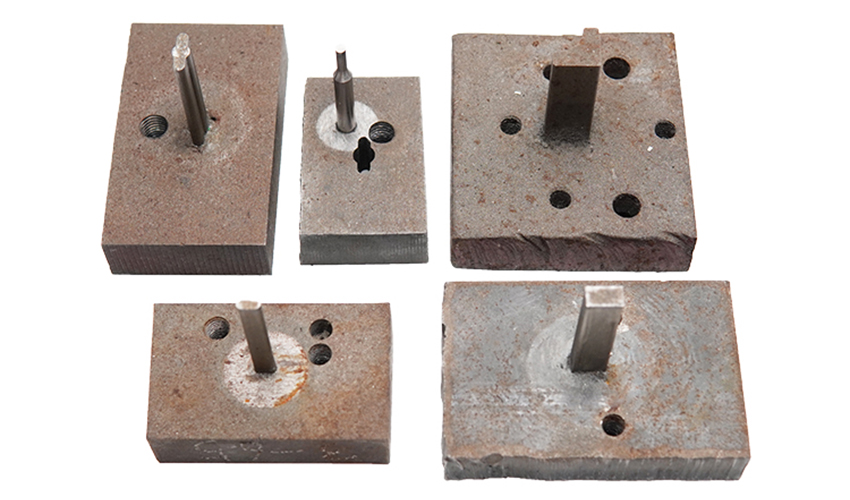
What is the difference between Aluminum Extrusion and Die Casting?
Die casting advantages includes forming complex shapes and irregular cross-section, while extrusion is limited to uniform cross-sections. Die casting is not constrained by sizes. Die casting allows cross-sectional changes or differentiation in the holes, slots, and any other design, whereas in the case of extrusion it requires secondary machining services on extruded parts that can be costly. Most products of die casting have greater stiffness value, or extrusion parts are more elastic. Die casting assures all features are produced directly through a one-step process of manufacturing. Also, die casting has a higher production rate, low part cost, less machining as it produced an end product with a one-step process, and is exceptional dimensional repeatability. Die casting are commonly used for bigger products such as boat propellers or larger part of engines.
However, extrusion has its advantages too, such as producing higher ductility of alloys like aluminum, magnesium, and zinc. These extruded parts may have the same strength and rigidity as those produced by die casting, but tooling costs are way cheaper in extrusion. Also, die costs are higher than extruded parts, and die construction takes up more time to change. In contrast with die casting, extrusion parts so no porosity while the other is more likely to be porous. Also, Aluminum extrusion surfaces can be directly used as the finished product, while surfaces of die casting require finishing.
Conclusion
Generally, in metal fabrication, we have to consider the method of manufacturing each of the parts. In our case, manufacturing of aluminum parts must require less cost, yet the parts must be machined from a solid to a near-net shape and still reduce the manufacturing time. We need a fast yet efficient way of metal fabrication, that will consider all the variables our customer needs.
