Die casting is an automated method of casting in which the molten metal is forced into a mold at a fast filling speed of up to 540 kilometers per hour while being subjected to high pressures ranging from 150 to 1200 bars.
In most cases, low melting point alloys are used in production. This form of casting utilizes permanent metal molds that are capable of being reused several times, as opposed to other casting methods, such as sand casting, in which the molds must be destroyed after each use. Large, intricate parts may be manufactured with little thickness.
TYPES OF DIE CASTING PROCESSES
The purpose of every variation on the die casting process is the same: to cast an object from a mold using molten metal injection. Several die casting procedures exist, each with advantages and disadvantages depending on the molten metal, component shape, and part size. These are the two primary die casting methods, including:
- Hot Chamber Die Casting
Injecting molds directly into the molten pool has the advantage of speed and convenience but at the cost of increased corrosion. Therefore, this method is ideal for high fluid, low melting point metals. Lead, magnesium, zinc, and copper can be used in this process.
- Cold Chamber Die Casting
Cold-chamber die casting is a great option when the immersion design of hot casting is ineffective due to corrosion. Casting aluminum and aluminum alloys are examples of such a case.
Die casting can be further subdivided into the following categories:
- Low-Pressure Die Casting Process
During this procedure, a riser tube connects the mold to the molten metal bath at a vertical height. The metal is drawn into a mold at a pressure of 20 to 100 kPa, releasing the chamber pressure. These high yields are achieved without feeders, a common component of high-pressure aluminum casting processes.
- Vacuum Die Casting Process
In this scenario, the cylinder chamber is evacuated, the molten metal is to be drawn into the mold. This layout lessens disruption and restricts the introduction of unwanted gas. The use of vacuum die casting is especially advantageous for components that will be subjected to heat treatment after they have been cast.
- Squeeze Die Casting Process
- Semi-Solid Die Casting Process
DIE CASTING ADVANTAGES
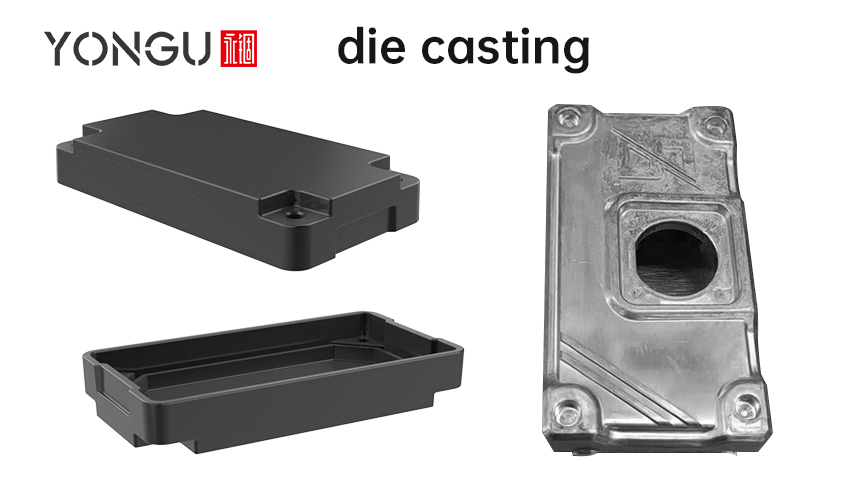
Die casting has several benefits over other manufacturing methods and can result in substantial savings, both in terms of the price of the item and the entire cost of production.
Casting a component allows you to make intricate net forms, such as external threads and interior features, with small draft angles and few secondary operations. Combining numerous elements reduces the need for assembly, saving time and money and facilitating easier stock management and higher component uniformity.
Other advantages include the following:
- Walls of varying thicknesses
- More stringent parameters
- Fewer processing stages between raw material and the final product
- Quick turnarounds during the manufacturing process
- Reduction in waste
- Zinc and magnesium have a very long life as tooling materials
Typically, die-casting alloys are made of zinc, aluminum, or magnesium. They are usually non-ferrous materials and have various mechanical qualities to suit multiple industrial uses. Die-cast alloys are entirely recyclable and can operate in extremely high temperatures. Die-cast alloys also have:
- High level of resistance to corrosion
- Extreme toughness and strength
- Excellent heat conduction
- High conductivity to electricity is a plus
- Perfect radio frequency and electromagnetic interference protection
- Exceptional qualities in terms of finishing
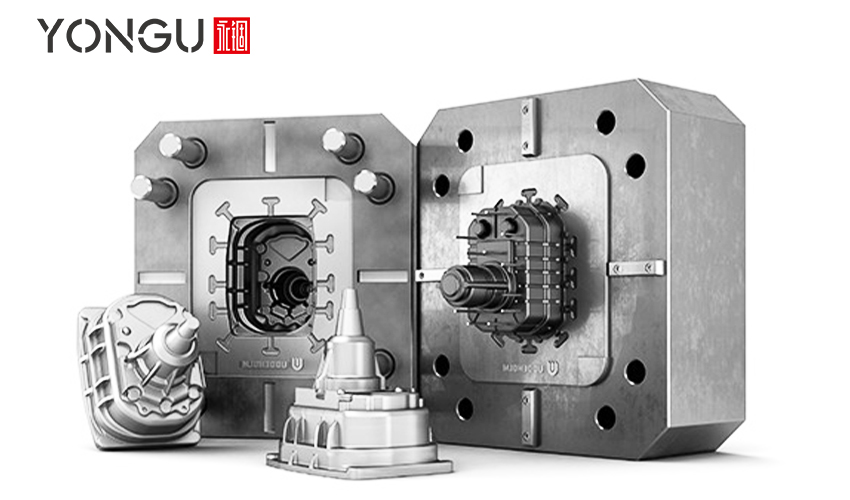
DIE CASTING APPLICATIONS
Die casting is often reserved for mass production runs, where numerous identical parts must be made. Even though much pressure is utilized in the casting process, the result is excellent. The die casting method creates lightweight, ultra-thin components that don't compromise on strength.
Wheels, cylinder heads, valve blocks, and manifolds are standard die-cast vehicle components. This sector comprises 84% of German foundries' castings. Aluminum reduces vehicle weight and fuel consumption.
In addition, die-cast parts are utilized in a variety of different sectors, including the following:
- Aviation
- Home Appliances
- Interiors
- Powered Equipment
- Electronics
- Machinist
- Household Appliances
YONGU DIE-CASTDIE-CAST END PANELS
YONGU is a market leader in producing electrical enclosures and is capable of designing and manufacturing custom die-cast electrical components. Our metal enclosures may be utilized for various purposes, whether your project requires thousands of units or just a tiny number to kick off a massive, long-term project.
One of the die-casted products of YONGU is YONGU Waterproof Electronics Aluminum Enclosure M05 200*75mm
It includes the following features:
- Aluminum Extruded Enclosure
- Die-Casting End Panels
- Integrated Silicone Sealing Ring
- Stainless Steel Screw
- Good Seal Screws Design
- Customized Holes Cutting And Milling
- Rail Transit
- Underwater Detection
- Outdoor Monitoring Equipment
- Color Customization
- Anodized Surface Finishing
- Customized Dimensions and Designing Service
For further information and customized product of your requirements, please follow our FACEBOOK for more updates and informations.
You can also contact us at +86 13326782625 or write us [email protected].