Systems designers want the relatively low costs and high availability of commercial off-the-shelf (COTS) technology despite the essential criteria for diminutive size, lightweight power consumption, extreme sturdiness, quick communication, and efficient thermal management. The design challenges faced by chassis manufacturers are substantial.
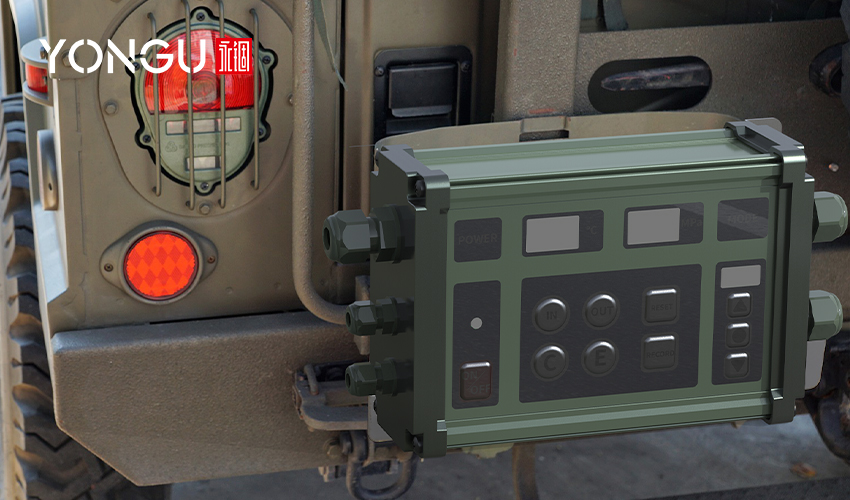
GENERAL APPROACH FOR MILITARY ENCLOSURES
Military advanced electronic enclosures are often highly engineered housing circuit boards for computation, input/output, data storage, and other system components. It is common practice to ruggedize these electronics enclosures to withstand shock, vibration, wide temperature fluctuation, and EMI effects.
When designing a system, it is up to the systems architect to choose which hardware components will work best for the intended purpose. For example, a small combat vehicle may require lightweight components with multiple input and output (I/O) connectors for the vehicle's many subsystems. It must be shielded from shock and vibration, and conduction cooling can be effective.
Conversely, a sizeable human-crewed aircraft can probably fit a typical air transport rack (ATR) box, which can have the capacity for high-performance rackmount servers and the fans required for convection cooling. Liquid flow-through cooling is one of the more out-there forms of thermal control that can be implemented in some ATRs.
Large systems like 6U VPX require space, weight, and power that ships typically don't have. For example, a 3U VPX system might be enough for the demanding processing needs of small platforms like jet fighter planes, which are sensitive to the size and weight constraints.
SWaP ANALYSIS
When choosing a chassis and enclosure, the systems designer must consider the system's size, weight, and power consumption requirements, or SWaP.
Light Weight Material
Military metal manufacturing requirements include precise tolerances, particular materials and finishes, and extensive destructive testing designed to survive the rigors of sea and battle.
Enclosures should therefore have a lightweight and high-strength feature that makes them simple to install and long-lasting. The ability to resist strain, such as stretching or compressing, is a measure of a material's strength. Contrarily, the material's toughness lies in its resistance to shock. Tensile or compressive strength typically increases, toughness decreases and vice versa.
For this reason, aluminum, a mixture of metals, is used to make most electrical enclosures for military defense systems. For similar reasons, the aluminum plate or structural steel used in defense system enclosures is often thicker (half an inch or three-quarters of an inch) and more expensive.
Weather Proof
Enclosures that are watertight and weatherproof safeguard the electrical and electronic components from dust and water elements in harsh environments. Guaranteed to withstand the elements for as long as needed, military-grade electronics require weatherproof enclosures and waterproof boxes that meet or exceed all applicable NEMA and IP standards and ratings. Electronic and electrical components are protected from moisture and dust in sealed enclosures with watertight gaskets.
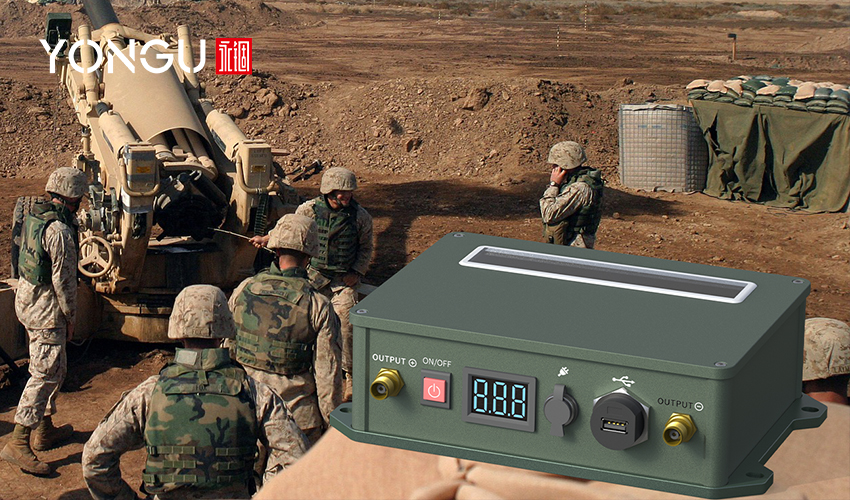
Cooling & Thermal Management
Customers prioritize the small size, lightweight, and inexpensive chassis and enclosures, but they also care deeply about thermal efficiency. High-performing electronics will inevitably produce heat, and excess heat is frequently blamed for performance drops and hardware problems.
Getting power into the system is not a problem, but venting the heat is. Regarding size, durability, and power consumption, conduction cooling is the only option for highly compact devices. Heat sinks, vents, and other components are required. It is inconvenient for everyone involved if rotary cooling requires waivers.
There are typically three distinct approaches to cooling and thermal management for chassis and enclosures, each of which addresses a unique set of circumstances.
Conduction Cooling
Eliminating the heat by shifting it away from the source.
Convection Cooling
Using a stream of air pushed by a fan to dissipate heat.
Liquid Cooling
The liquid is flowed through overheated parts or sprayed over circuit boards and housings to remove heat.
Conduction cooling, which takes up little room, needs no additional power, and is intrinsically robust, is often the simplest solution, especially for SWaP-constrained systems.
Conduction cooling is the most cost-effective method of thermal management for rigid systems. However, it does require additional components like metal card edges and fins on and surrounding boards to dissipate heat to the outside of the chassis or enclosure.
However, conduction cooling can't handle the heat produced by some effective systems. For this purpose, engineers often turn to blown air systems powered by fans, employing various techniques for directing the blown air.
Several problems might arise when using blown air in military embedded systems, so designers try to avoid it whenever possible. To begin, the cost of convection cooling is often higher than that of conduction cooling. Fans are moving parts and, therefore, prone to failure and regular maintenance, which presents a problem for durability and upkeep. Thirdly, if a fan stops working unexpectedly, it could cause a chain reaction of failures. Finally, in comparison to conduction cooling, fans take up more room and use more energy. To make the most of blown air, designers must also create reasonably open air routes.
Even convection-cooled military embedded systems can't handle the heat produced by the most powerful of these devices. That's why high-end microprocessors and other heat-generating component systems need liquid cooling.
I/O and connectivity
Today's chassis and enclosures for military and aerospace should provide options for multiple designs, connectivity, and I/O to support the most extensive range of rugged applications. Off-the-shelf options, value-added options, and fully tailored solutions should all be available for these problems.
As a result of the delicate balancing act between low cost and excellent performance, COTS is typically the first option considered by system designers.
VPX is quickly replacing VME and Compact PCI as the preferred interface for designing robust military embedded devices.
VPX is widely used because it supports multiple input/output (I/O) types and interface speeds (RF, fiber optic, and more). These demanding aerospace and defense applications have helped propel the adoption of VPX, which is available in both 6U and 3U form factors. It provides the ability for future updates, is robust, and is commercially accessible. It also supports several cooling and thermal management strategies.
However, those aren't the only benefits of VPX. The current versions offer a throughput of 16 Gbps per channel, with future versions predicted to deliver at least 25 Gbps per channel. In addition, VPX may now support optical transceivers, giving engineers a choice between copper and optical fiber for data transmission.
CONCLUSION
Defense and military systems require enclosures and rack mount chassis that can work reliably in the harshest conditions on land, sea, and air. As such, they must be built to withstand the worst weather, humidity, dust, and other threats.
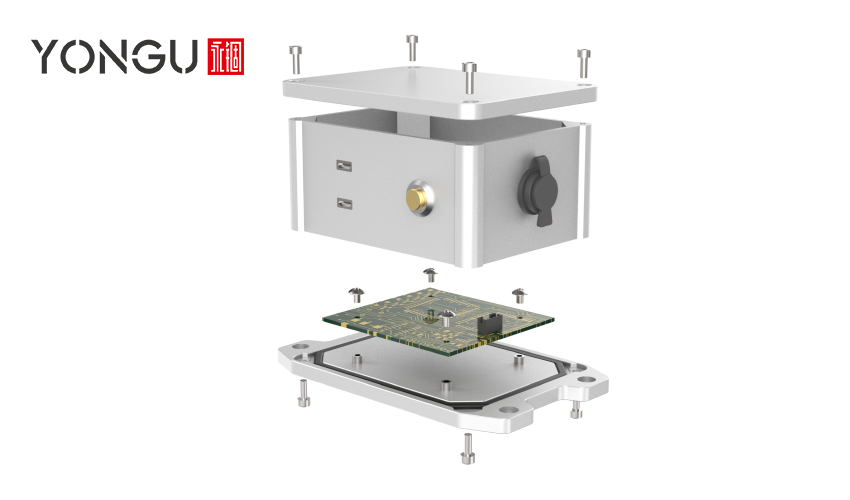
YONGU CUSTOMISED ENCLOSURES DESIGNED FOR MILITARY AND AVIONICS
YONGU is here to assist you in constructing your military-quality enclosure, whether you are just getting started or want some direction. The process begins with examining the intended use, followed by an outline of the optimal enclosure layout in CAD. We can fulfill OEM and ODM requests. If you want your prototype to stand out from the crowd, we can help you modify its structure and appearance.
Options for customization of any design, size, and material are available for all YONGU products, which include Rackmount Enclosures, Instrument Enclosures, Aluminum Enclosures, Amplifier Boxes, Desktop Enclosures, Medical Device Enclosures, Panels, Machine Foots, Rack Handles, and many more. With our cutting-edge equipment and professional workforce, we can design and weld any plastic, aluminum, or other material enclosure that a client may require.
We can help you create a prototype of your idea or an entire production run. YONGU aims to tailor the system's construction and operation to your requirements by employing Multi-Disciplinary Optimization methods.
One of the services YONGU provides is the processing of high-quality boxes. It will help if you put your efforts into promoting accurate supply networks instead of developing frictionless technologies.
YONGU can assist in producing Military Grade Electrical Enclosures following the specifications and drawings provided by the client. The finished products will be impervious to EMI radiation, dirt, moisture, and grit. Complex machining, sealing, and assembly is integral parts of the enclosures' design. Cards holders, doors, and latches are a few examples of the countless personalization options available.
The minimum we offer in our customized enclosure for military-grade systems includes
- Lightweight, Frame-Supported
- The coating that is resistant to rust and mold
- Robust Mechanical Design
- Efficient Cooling Solutions
- Customized Sizing Options
- Board Capacity Options
- Easy Assembly
- NEMA & IP Rated Protection
For further information and customized product of your requirements, please follow our FACEBOOK for more updates and informations.
You can also contact us at +86 13326782625 or write us [email protected].