Engineers and manufacturers have begun to understand the significance of medical device electronic enclosures design after years of experience designing integrated electromechanical systems. Whether you're working on a control panel for a factory or a wearable medical device, an attractive and reliable plastic electronic enclosures is crucial to your success.
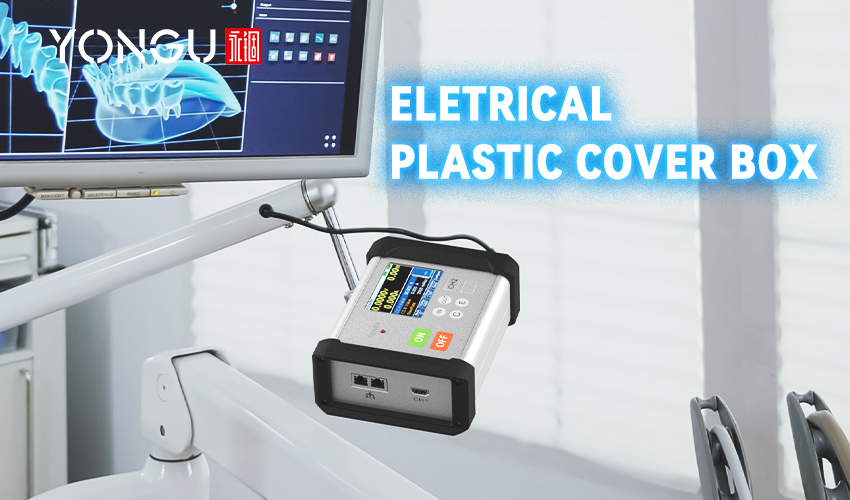
KEY DESIGN FEATURES OF MEDICAL ENCLOSURES
Toughness & Resilience
Stronger-than-expected construction is required for medical custom electronic enclosures. Please don't assume that because they spend their entire lives in a friendly, warm, air-conditioned hospital, they'll have it easy.
There will be no let-up in the volume of use of medical devices over a year. Hospitals cannot afford to stock their shelves with electronics that will only see occasional use. Therefore, this machinery needs to be able to cope with a demanding schedule and be handled by a wide variety of healthcare personnel, almost all of whom will be working under pressure.
Ergonomics
Any contemporary custom electronic enclosures needs this, but the medical field needs even more. All medical storage units should be designed with a focus on contours. Not only does this make them more pleasant to use, but it also makes maintenance a breeze compared to a series of sharp corners. Keep in mind that patients will need to operate these machines in addition to doctors and nurses. Because some of these people may have mental or physical disabilities, simplicity of usage is essential.
Easy Cleaning
In the era of antibiotic-resistant superbugs plaguing hospitals today, infection prevention and control have become crucial. Health care facilities know the dangers of healthcare-associated infections, which can be spread by direct patient-to-patient contact or by contaminated medical equipment. It necessitates making electronic enclosures out of glossy plastic that is simpler to disinfect and wipe out.
Security
Tamper-proof construction is required for all medical custom enclosures. That entails employing Torx assembly screws as the default option.
Aesthetics
It is a crucial consideration. It is not enough for medical gear to work well; it must also look attractive and maintain that aesthetic. If you were a patient, how would you feel if the electronics helping you get well were encased in a plastic electronic enclosures that looked old and worn? It is hardly something that would inspire confidence.
Standards & Testing
Commercializing medical electronics is subject to several local and global laws and guidelines. However, these norms and regulations might vary widely depending on who designs the product and where it will be used.
Specifications for various parts of a medical enclosure can vary. For instance, the UL 94v-0 standard for flame resistance may be required, or perhaps the plastic needs to be capable of a high level of sterilization. Because of the potential for bodily fluids and other liquids to disrupt electronic circuits in a medical environment, IP 65 and NEMA 4 waterproof electronics enclosure are recommended.
Certification Bodies may conduct various tests for medical enclosures, including those for flammability, EMI/RFI, UV Stability, Shielding effectiveness, Shock, vibration, seismic, Thermal, airflow, cooling modeling and analysis, and other environmental tests.
The final application, the extent of post-manufacturing work on the electronic enclosure, and the end customer's needs will all influence the number and nature of tests conducted. Products must be tested in their intended final form before release. As the final design often involves electronics and other components integrated by the original equipment manufacturer (OEM), much of the testing performed by the electronic enclosures manufacturer is irrelevant.
Much original equipment manufacturer (OEM) clients will demand that an enclosure be either "designed to meet" or be tested to satisfy certain criteria. It is done to ensure that the finished assembly will pass any testing necessary for the application.
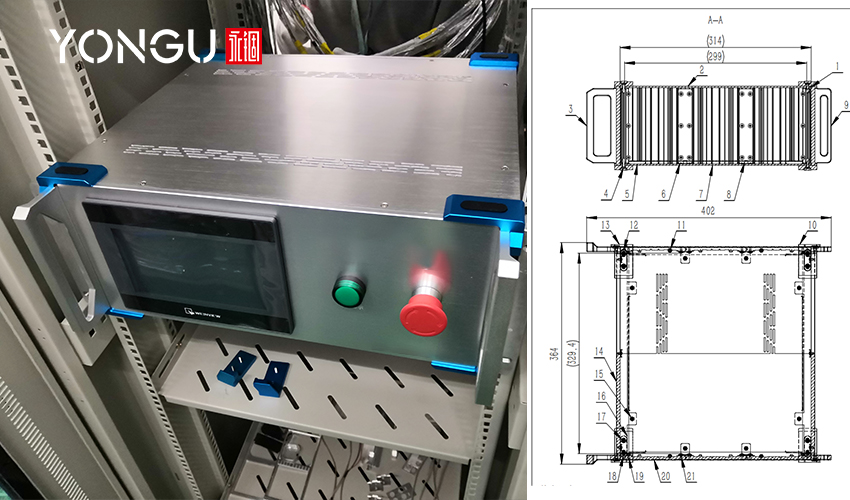
Materials
Most enclosures are made of steel, plastic, or fiberglass. As the unit's purpose and cost/benefit ratio are considered, so is the material chosen.
The versatility of plastic molding allows manufacturers to create a wide variety of attractive medical enclosures. While ABS can be molded into medical electronic enclosures, ASA is preferable due to its excellent UV stability. Or, even better, a less flammable ASA blend like ASA+PC-FR incorporates polycarbonate for extra robustness.
Steel is the material of choice for heavier load-bearing in bigger enclosures. Sometimes the selection will be based on the designer's taste or marketing factors.
YONGU MEDICAL FIT ENCLOSURE DESIGNS
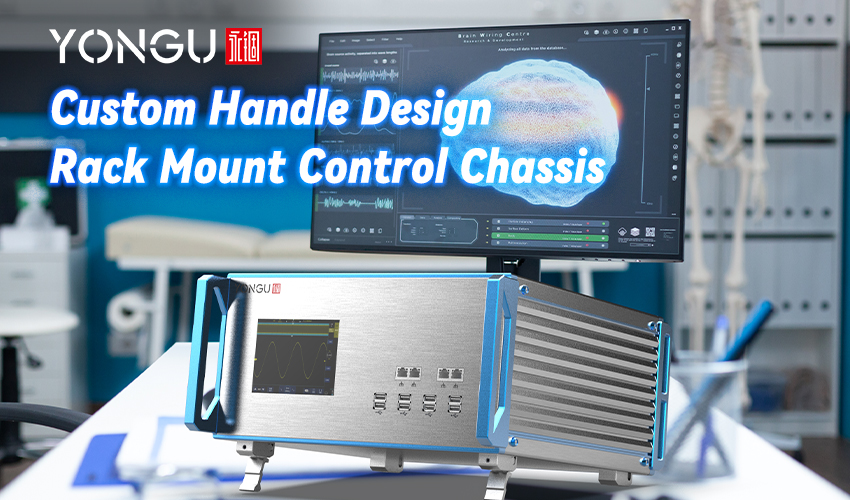
Durability and careful engineering are essential for diagnostic equipment, whether it's used in the medical field or any other setting where a highly utilized workstation is required. The supply chain as a whole is multifaceted and must conform to these principles.
By constructing the necessary enclosures and performing the final assembly, YONGU is pleased to contribute to the production and eventual success of the product. Because of our expertise in customized aluminum and plastic electrical and electronic enclosures, we can anticipate the difficulties that medical equipment may meet in actual use.
We take into mind more than merely providing robust features while creating electronic enclosures. For construction and operation, electronics, controls, and hardware must be considered. In addition to being easy to fix and upgrade, a well-thought-out design will also facilitate these tasks.
Moreover, we accommodate the operator's ease of use and mobility and account for other ergonomic concerns. After the design has been thoroughly evaluated and approved and a precise production method has been put out, YONGU will begin fabricating custom plastic enclosures for your medical equipment or suggest our shelf designs.
The success of the products we make at YONGU relies heavily on our ability to offer advice and apply our extensive expertise in custom manufacturing and materials.
Plastic electrical enclosures with an Ingress Protection rating are available from YONGUBOX in a wide range of standard and custom configurations. We are pleased to provide a variety of options for electronic enclosures, such as those used in medical devices and other fields:
K Series include different 27 different models, among which few are
- YONGU Aluminum Plastic Pannal Electrical Box K23C 200*55 mm
- YONGU Electrical Plastic Cover Box K21C 160*55 mm
- YONGU Custom Plastic Cover Electrical Box K22C 180*45 mm
- YONGU Plastic Pannal Custom Split Enclosure K19C 140*50 mm
- YONGU Protected Plastic End Panel Aluminum Enclosure K09 152*44 mm
They have the following properties in common
For further information and customized product of your requirements, please follow our FACEBOOK for more updates and informations.
You can also contact us at +86 13326782625 or write us [email protected].
- Waterproof, dust-proof, and resistant to collisions
- Offers a customized design service
- <lt;span style="line-height:150%">The ability to tailor the drilling of holes
- Anodizing is provided in a range of hues
- Laser etching and silk screening
- Dust-proof and impact-resistant facade panels
- Enhanced ability to dissipate heat
You can also contact us at +86 13326782625 or write us [email protected].