Extrusion is the process used for extracting aluminum. It is similar to a toothpaste squeezed out of a tube.
Around the world, the aluminum extrusion market is rapidly increasing. A report by Technavio shows that this industry will accelerate at a Compound Annual Growth Rate of 5.02% in 2021-2025. Thus, this could reach 8.87 million tons. This enables the metal industry to prosper even amidst the COVID-19 pandemic.
Moreover, extrusion has numerous uses in architecture, automotive, electronics, aerospace, energy, and other industries.
In China, there is a higher demand for aluminum because of some of the significant reasons published by FxEmpire.com:
● China’s huge growth and urbanization– Known for its large size, population, and generally less developed economy, it has the potential to grow. The Communists government is making sure they use this potential. Many cities have come up in China. The housing industry has taken off. This increases the consumption of aluminum both for construction and also for household use. It resulted in prediction models for the metal prices to show a gradual increase over the years
● The China government has programs for all fields of development in infrastructure, space, housing, etc. They have huge investments into these programs with their sophisticated mechanisms. They can predict the metal prices and can control their supply and demand in aluminum
● For a decade or more, the exports of aluminum in China have been booming. China exports a range of stuff ranging from small-scale to large-scale transactions. Buyers preferred them for their low prices and decent quality. Aluminum is a vital raw material for many products
All products undergo a process. Aluminum extrusion happens when profiles are pushed through a die and forms the shape of the opening of a die.
So, here are the ten steps to understand how it takes place.
Step #1: Preparing Extrusion Die and Moving to the Extrusion Press
A round-shaped die is machined to H-13 steel unless there is a ready-to-use one. Preheating is very important before extrusion. Tune at 450-500 degrees Celsius to ensure the life of the alloy. This makes the flow of metal even. After preheating the die, it is now ready to be loaded into the extrusion press.
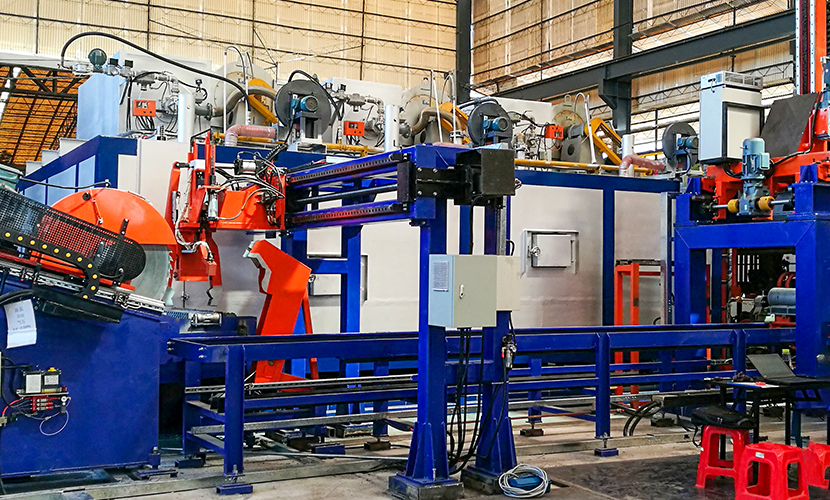
Step #2: Preheating Aluminium Billet Before Extrusion
A billet is a solid, cylindrical block of an aluminum alloy. It is preheated in an oven between 400-500 degrees Celsius after being taken from a longer log of alloy. Thus, resulting in a suited level of malleability for the extrusion process.
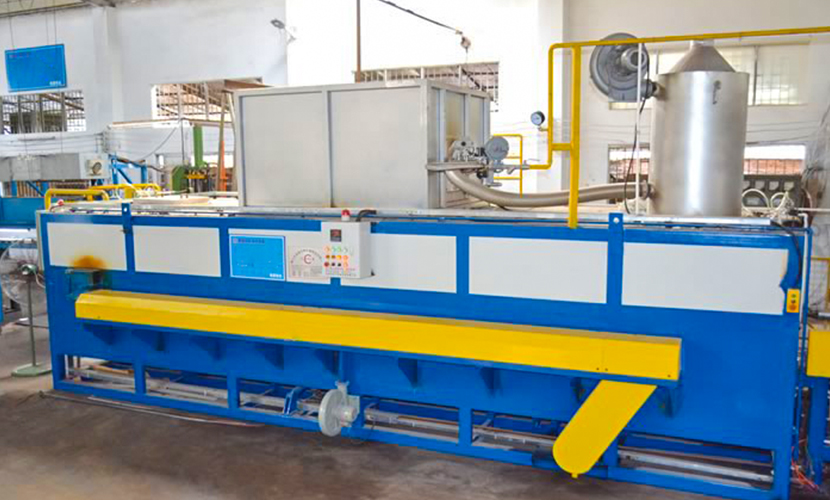
Step #3: Transferring the Billet to the Extrusion Press
After preheating the billet, it is moved mechanically to the extrusion press.
A lubricant (release agent) is applied to the billet and to the ram to prevent them from sticking together. Then the billet is loaded onto the press.
Step #4: Forcing the Billet Material into the Container using the Ram
In this step, a hydraulic ram exerts up to 15,000 tons of pressure as the extrusion press is loaded with the malleable billet. The billet material is then pushed into the container of the extrusion press as the ram applies pressure. Finally, the material is visibly expanding to fill the walls of the container.
Step #5: Coming out of the extruded material through the die
In this stage, the alloy is being pressed against the extrusion die as it fills the container.
The aluminum material is sealed with continuous application of pressure.
Then, as it comes out from the die’s opening, a profile is formed.
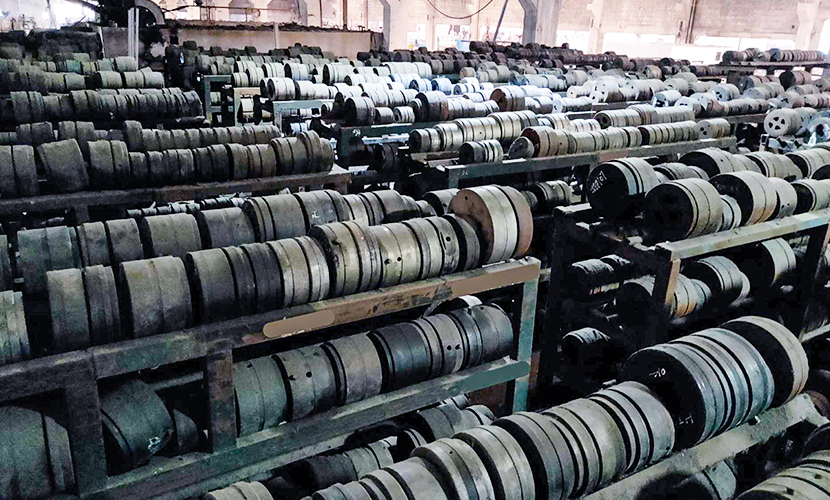
Step #6: Enabling a Smooth Exit of the Extrusion from Its Press
This time, a puller is used to grip and guide the smooth exit of the extrusion from the press.
Then, the profile is evenly cooled by a water bath or by fans above while moving along the runout table.
Step #7: Cutting the Extrusions to Mill- Length
Temperature is essential in every step.
The next step is now shearing by a hot saw to take it from the extrusion process as the extrusion completes its full table length. Despite having a cooling process after exiting the press, the extrusion is not completely cooled.
Step #8: Quenching the Extrusions
Mechanically, mill-length extrusions are moved separately from the runout table to a cooling table. As the profiles reach room temperature, there is a need to be stretched.
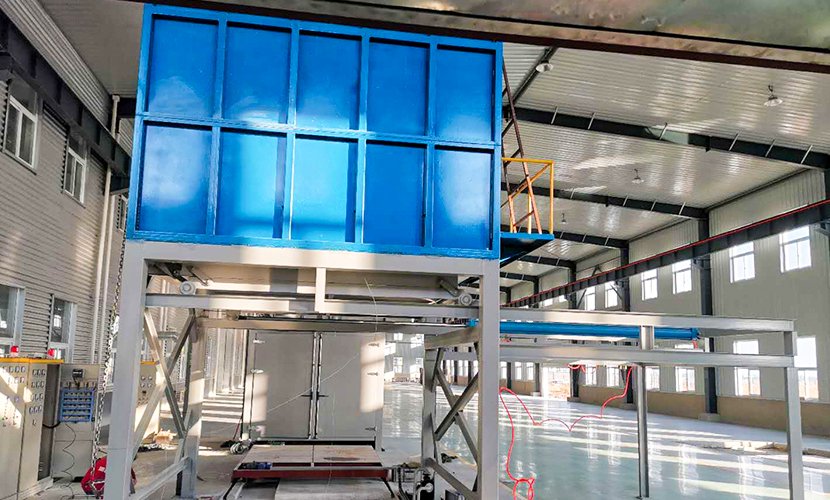
Step #9: Moving the Extrusions to the Stretcher and Aligning them
The profiles have some natural bending that needs to be corrected. Hence, these are moved to a stretcher. Both ends of the profiles are gripped mechanically. These are being pulled until they become completely straight and placed for specification.
Step #10: Moving the Extrusions to the Finish Saw and Cutting to Length
Once extrusions are cut table-length and hardened, these are moved to the saw table. This time, sawing to pre-specified lengths is done usually from 8-21 feet long.
Now, the T4 temper matches the properties of the extrusions. The next part is to move them to an aging oven to reach the T5 or T6 temper.
After Extrusion: Heat Treatment, Finishing, and Fabrication
The heat treatment takes place to enhance the properties of the profiles. After this, profiles can be applied with different surface finishes to produce a better appearance and corrosion protection.
Final dimensions can be done using fabrication operations.
Heat Treatment
Aluminum heat treatment is a process which increases the the strength and hardness of an alloy. Usually, 2000, 6000, and 7000 series can be heat treated to reach its highest tensile strength and yield stress. These are achieved by putting profiles into ovens where their aging process are hastened and brought to T5 or T6 tempers.
Customers need to understand the needs of their project to ensure the right choice of alloy and temper.
As the heat treatment is done, profiles can also be finished.
Surface Finishing: Enhancing Appearance and Corrosion Protection
There are a number of different finishing operations for aluminum profiles.
Enhancing the appearance and the corrosion properties are the two main reasons.
There are other finishing processes that can be done such as painting, powder coating, sandblasting, and sublimation.
Furthermore, profiles can be altered in different ways to match your specifications. These can be punched, drilled, machined, or cut. Achieving the final dimensions of the profiles can be customized.
This means that extrusion has many fabrication options.
Benefits of Aluminum
As alloys went into the surface, many innovations were made and invented.
Aluminum products can minimize energy costs and carbon emissions in many forms of applications. It has been proven that coated aluminum roofs can reflect up to 95 percent of sunlight which contributes to increasing building energy efficiency.
From the convenience that it gives, it is also the sustainable material of choice in many markets. Hence, most of the products that we use today either contain aluminum or are made up of aluminum. Aluminum is the answer in the quest towards a more fuel-efficient future.
Yongu has been in this industry for many years and most of our products undergo a process of aluminum extrusion. To know more about our products and how we can best serve you, check out our website at https://www.yg-enclosure.com or email us at [email protected].